Aluminum Profile Guide: What are standard aluminum extrusion profiles?
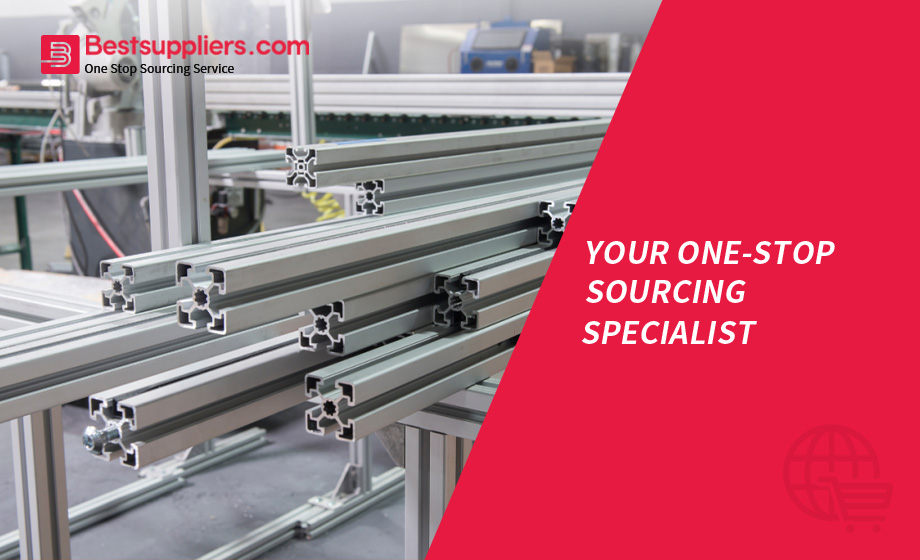
Have you ever heard about extruded aluminum profiles? In recent years, aluminum extrusion profiles have become increasingly popular in product design and manufacturing. But what exactly are they, and how does the process work? Let's learn more about standard aluminum extrusion profiles on Bestsuppliers.
What Are Standard Aluminum Extrusion Profiles?
An aluminum profile, also known as aluminum extrusion, is created by the process of pushing heated aluminum materials through a die with a desired cross-section, resulting in a specific shape or profile. As a lightweight, corrosion-resistant aluminum material, extruded aluminum profiles are widely used in a variety of machine frames and industrial applications. Besides, aluminum extrusion profiles can be further processed to create finished products such as doors, windows, and curtain walls for the building and construction industry, as well as heat sinks and enclosures for electronics and lighting applications.
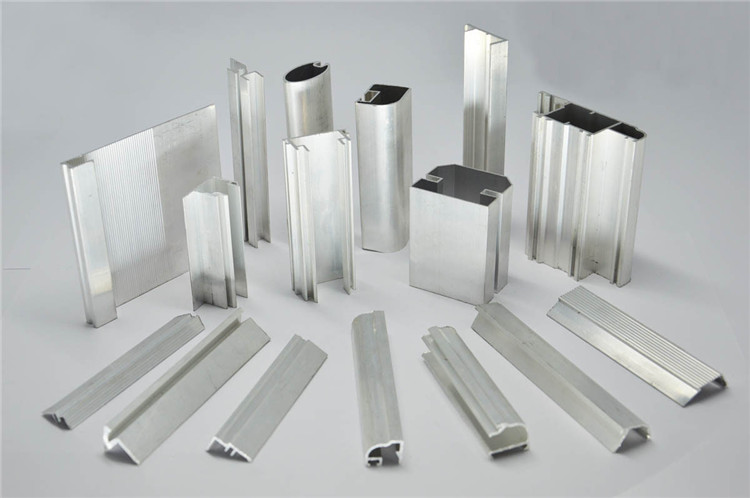
Profile aluminum can be produced in various shapes, sizes, and thicknesses to meet the requirements of different applications. There are some standard aluminum extrusion profiles available, including but not limited to:
- Square and rectangular tubes
- T-Slot profiles
- Round tubes and pipes
- Angle profiles
What Are the Different Types of Aluminum Profiles?
Types | Characteristics | Applications |
Hollow Beam | Aluminum beams that lack specific cross-sections are useful in providing horizontal support. | Usually used as a support framework for buildings, and bridges. |
Square Profile | It can be easily fabricated, cut, and joined to create a variety of structures and assemblies. | Commonly used in industrial and construction applications |
SD Aluminum Profile | Flexible and lightweight; characterized by corrosion resistance and weather resistance. | An ideal aluminum extrusion profile for windows and doors. |
RCW Profile | Acts as a barrier that prevents environmental elements from entering a building. | Commonly applied to curtain walls and mullions. |
Door Section | Known as an ED section, it provides a secure means of holding glass material in place, preventing it from falling or toppling suddenly. | A glass aluminum profile is used in heavy-duty glass doors. |
Louver Profile | An arrangement in which slats are attached at regular horizontal intervals at an angle to one another. | Used for natural lighting and ventilation. |
T-Section | T-shaped aluminum extrusions; providing support in various directions. | Used in a corner or as part of a truss network. |
What Are the Different Aluminum Extrusion Shapes?
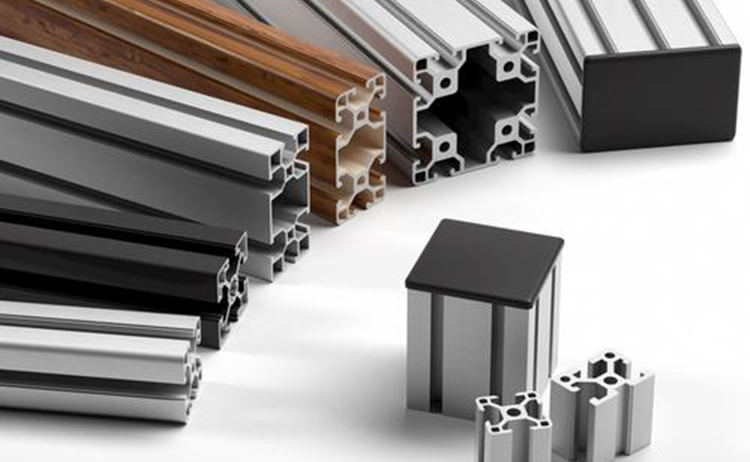
There are numerous aluminum extrusion shapes available, and the following are some of the most common:
- T-Slot Extrusions: These have a T-shaped groove on one or more sides, making them ideal for structural frames, enclosures, and modular workstations.
- Rectangular Tubes: These have a hollow interior with straight sides and flat edges, making them ideal for structural applications such as framing and supports.
- Angle Profiles: These are L-shaped extrusions that are used to join two panels or surfaces at a right angle.
- U-Channels: These U-shaped extrusions are used to cover and protect the edges of panels or surfaces.
- I-Beams: These have a vertical central web with flanges on either side, resulting in an I-shaped cross-section. They are used in high-strength structural applications.
- H-Beams: These are extrusions with two horizontal flanges on either side and a vertical web in the middle, resulting in an H-shaped cross-section. They are employed in heavy-duty structural applications such as bridge construction.
- Round Tubes: These extrusions, which have a circular cross-section, are commonly used in applications that require a lightweight and rigid structure, such as tent poles or flagpoles.
Benefits of Extruded Aluminum Profiles
As a fascinating material, the aluminum extrusion profile offers several advantages, including:
Lightweight
Compared with other metals, aluminum is much lighter, which means it is more manageable and less expensive to transport. As a cost-effective option for applications, the extruded aluminum profile also offers a higher strength-to-weight ratio, reducing the overall weight of the final product.
Corrosion Resistance
Excellent corrosion resistance is essential for some applications involving outdoor or marine environments. Aluminum extrusion profiles are naturally resistant to corrosion and do not rust. Because their surface is covered by an oxide film.
High Thermal Conductivity
Aluminum's ability to conduct heat rapidly is a valuable characteristic that makes it suitable for various applications, such as cookware, extruded heat sinks, and emergency fire management. In the case of fire management, long enough extrusions can conduct heat away from the fire, helping to regulate temperatures.
Excellent Electrical Conductivity
Extruded aluminum profile is an ideal material for projects involving electricity as it shows a significantly higher electrical conductivity than other materials (such as copper), while also being less expensive.
Versatility and Durability
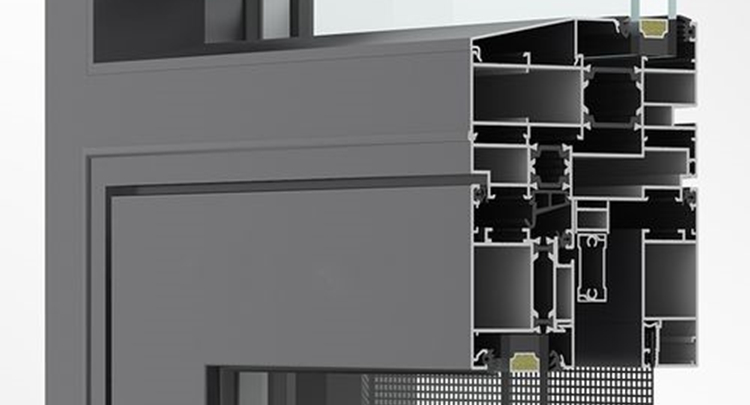
Aluminum extrusion profiles can be produced in a wide range of shapes and sizes, making them suitable for a variety of applications. At the same time, they’re durable and can withstand exposure to extreme temperatures, weather conditions, and harsh chemicals.
Environmentally Friendly
The extruded aluminum profile is a recyclable material. The energy required to recycle aluminum is much lower than that required to produce new aluminum, making it an eco-friendly option.
The Aluminum Extrusion Process in 10 Steps
Step 1: Designing the product
The first step in the aluminum extrusion process is designing the product or component. The design determines the shape, size, and other specifications of the final product.
Step 2: Getting the die ready
The second step in the aluminum extrusion process is to create the die to meet the design specifications. The die is made from steel and is customized to the specific shape and size of the product. Then, heating the die to a temperature range of 450 to 500 degrees Celsius before the actual extrusion.
Step 3: Preheating the aluminum billet
The aluminum billet, which is a cylindrical shape of aluminum alloy, is cut to the required length for the extrusion process. After that, put the billet in the oven and preheat it at the same temperature as the die. This heating process makes the billet pliable but not yet liquid.
Step 4: Transferring the billet to the extrusion process
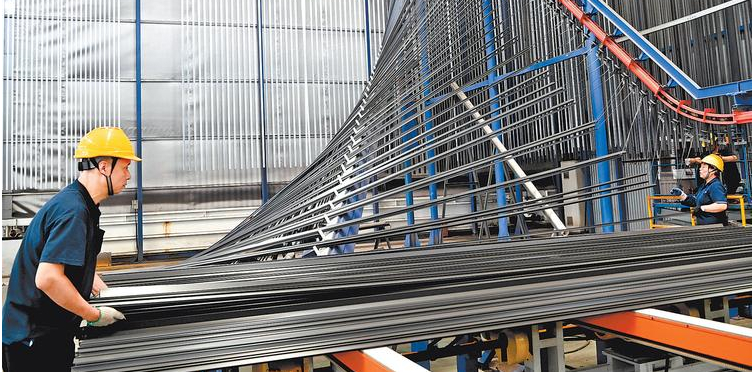
After being lubricated, the heated billet sh loaded into the extrusion press, where it is pushed through the die using high pressure. The extruded material takes the shape of the die, creating the desired profile.
Step 5: Quenching the materials on the runout table
The next step involves transferring the extruded material from the die to the runout table where it undergoes cooling. This can be done using a water quench or air-cooling system to help it maintain its shape and strength.
Step 6: Shearing the Extrusions to table length
Once the extruded material has achieved its full table length, it is separated from the extrusion process by being cut with a hot saw. However, the material has not completed its cooling process and needs further treatment.
Step 7: Cooling the extruded materials
The next stage in post-production is to cool the alloy to room temperature. The extruded aluminum is supposed to be transported to a cooling table where it will be left until it has reached the standard temperature.
Step 8: Stretching the extruded aluminum profiles
After cooling, the aluminum extrusion profiles must be placed on a stretcher and undergo stretching to smooth out any distortions.
Step 9: Sawing and cutting
After completing the previous steps, the next step is to see the extruded material into specific sizes. Once sawed, the material is put into an aging oven for tempering to reach either the T5 or T6 tempers.
Step 10: Finishing and fabrication
The profiles may undergo additional finishing processes, such as surface treatments or coatings, to improve their appearance and durability. Also, the finished profiles may be further processed or fabricated into finished products, such as doors, windows, and other building components.
Conclusion
Due to its outstanding performance, the extruded aluminum profile is an immensely appealing material. If you're considering aluminum extrusion profiles for your upcoming project, feel free to consult with us for advice on Bestsuppliers.