How to Ensure and Improve Your Solar Panel Quality
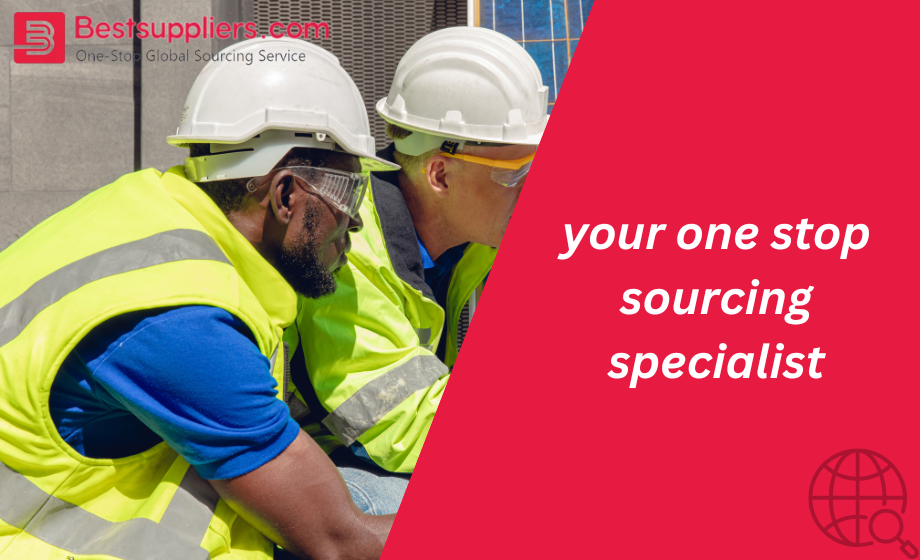
Solar energy is becoming more popular as the world seeks more renewable energy sources. Countries around the world are tapping into the advantages of solar power, which drives up the demand for high-quality solar equipment and components. However, finding solar equipment can be difficult. Especially because the solar panel production cycle is complex, with different stages such as choosing raw materials, assembling cells, and assembling modules, each stage has important quality parameters that need to be checked. Moreover, unreliable suppliers offering low-quality products make quality inspections more essential than ever. This guide will teach you everything about solar panel quality checks and reveal our insider tips on the most frequent defects found during inspections
Why solar panel quality check is needed?
A solar panel quality check is needed to ensure that the solar panels meet the required performance, safety, durability, and compliance standards. Quality checks can help detect and prevent any defects or issues that may affect the solar panels’ effectiveness and lifespan. Quality checks can also help reduce the risk of electrical hazards, warranty claims, and customer complaints. If you want to learn more about solar panel quality checks, you can check out the web search results I found for you. They provide some useful guides and tips on how to check the quality of solar panels during production, inspection, and maintenance.
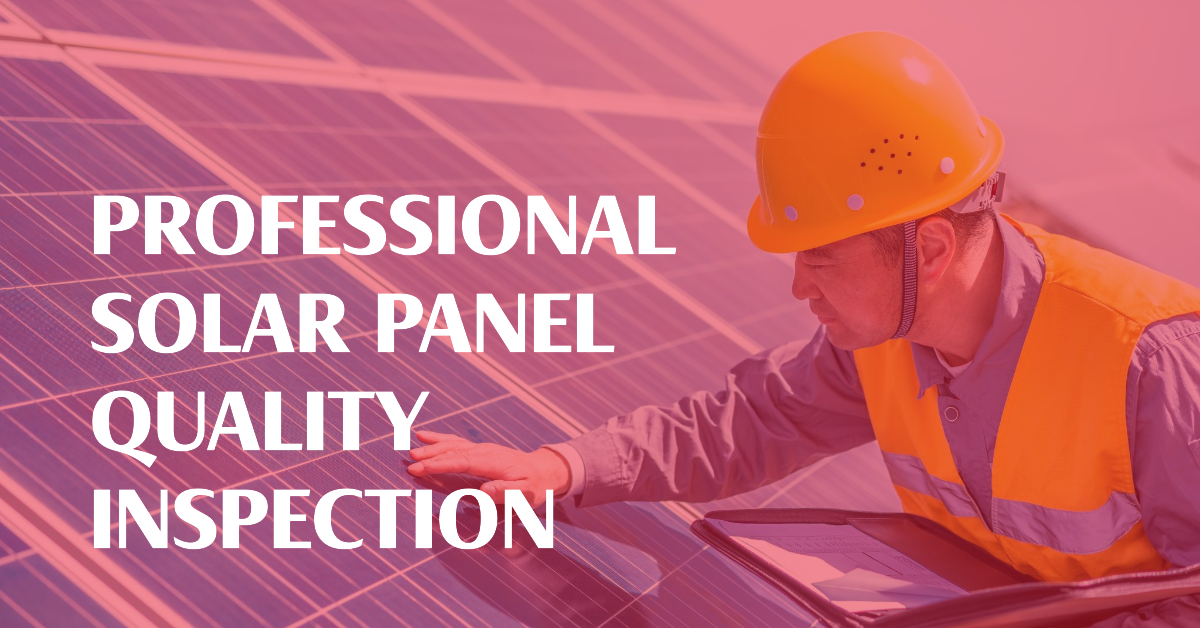
How to check solar panel quality during production?
Solar panel quality check is a process of inspecting the materials, workmanship, performance, and documentation of solar panels to ensure they meet the required standards and specifications. Solar panel quality checks can help you avoid any defects, issues, or hazards that may affect the solar panels’ efficiency and lifespan. the solar panel quality check covers various parts, some of the common steps include:
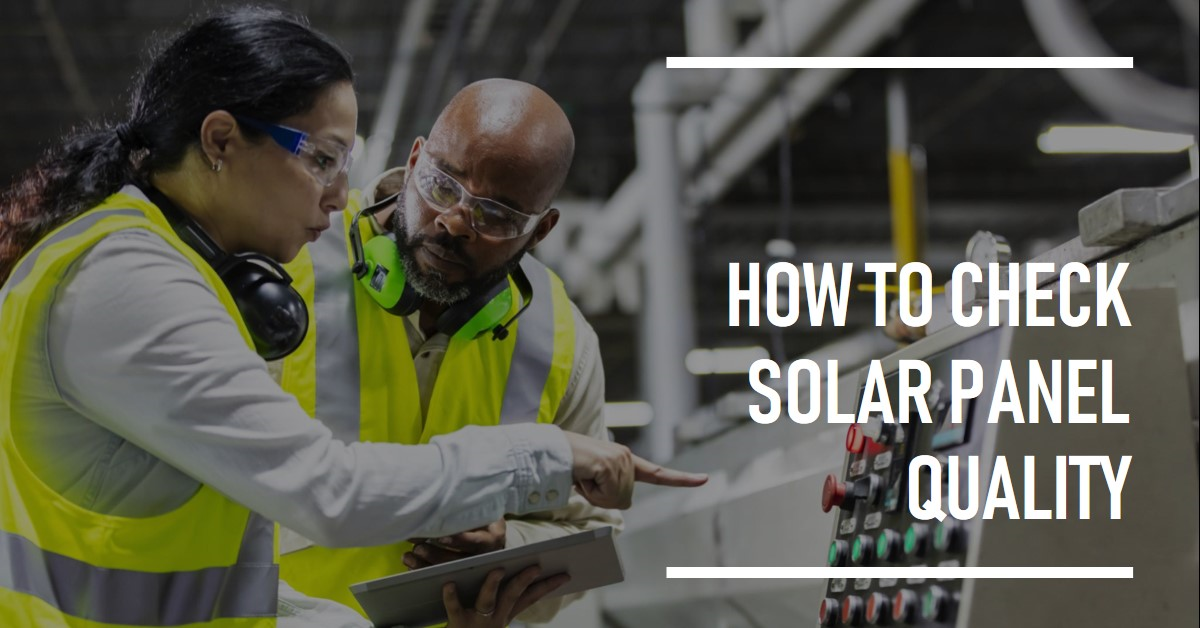
1. Assessing the workmanship of the panels, such as the appearance, dimensions, labels, and connections.
During the evaluation of the case and specifications, an inspector would examine samples of the products using Acceptable Quality Limit parameters. The inspection generally involves factors such as Visual Inspection: Visual inspection of solar panels involves looking for visible defects, such as cracks, discoloration, scratches, or dents on the solar module, as well as any irregularities in the framing or glass, junction box, and wiring. Labeling and Alignment: Confirm product labeling and the alignment of the photovoltaic panels to ensure they comply with the quality standards. Product Dimensions: Check if the product dimensions match the specifications
2. Checking the documentation of the panels, such as the certificates, manuals, and warranty.
The inspector would check the manufacturer’s documentation to ensure that the products comply with the required quality standards and regulations, such as product certifications and other conformity labels like BIS certificate, IEC, UKCA Marking, CE mark, and Underwriters Laboratories (UL) marking. The inspector would also review any relevant manuals or technical documents.
3. Field Test and Measurement of Solar Equipment
The inspector may perform electroluminescence testing, calibration, and solar STC, depending on the type and availability of equipment at the factory. Electroluminescence Testing/EL Test: A non-destructive testing method to check the quality of photovoltaic panels for microcracks and other anomalies that may not be seen by the eye. Solar Module Calibration: Measure the panel’s electrical parameters and confirm that it produces the expected amount of electricity under various conditions. Solar STC (Standard Testing Conditions): Measure the solar panel’s output voltage and current under standard testing conditions to ensure the best performance
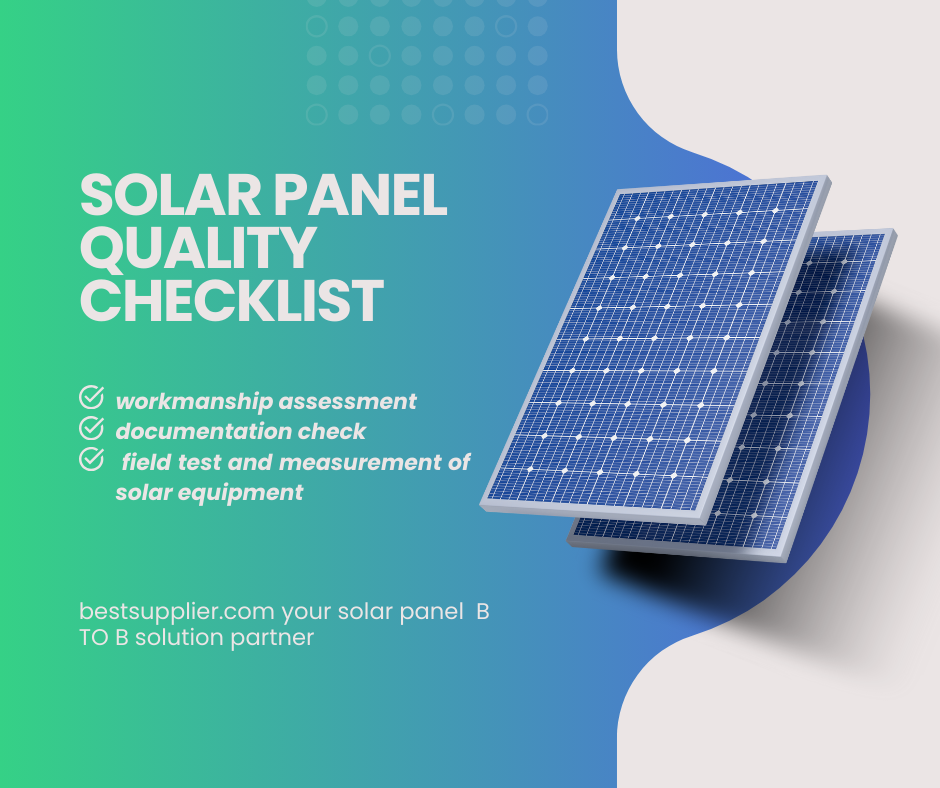
What are the common defects found in solar PV Inspection?
Solar PV inspection is a process of checking the quality and performance of solar panels to ensure they meet the required standards and specifications. Some of the common defects that may be found during solar PV inspection are:
- Cell defects: These are cracks, broken fingers, or dead cells that affect the efficiency of the solar panels. They may be caused by poor manufacturing, handling, or installation.
- Hot spots: These are areas on the panel that become significantly hotter than the surrounding areas. They can lead to permanent damage and reduced panel performance. They may be caused by shading, dirt, or faulty wiring.
- Discoloration: This is a change in the color of the solar cells or the back sheet. It can indicate degradation or corrosion of the materials. It may be caused by exposure to moisture, heat, or UV rays.
- Delamination: This is the separation of the layers of the solar panel. It can reduce the protection and insulation of the panel. It may be caused by thermal stress, mechanical stress, or moisture ingress.
- Snail trails: These are dark lines or spots on the surface of the solar cells. They can reduce the power output and aesthetic value of the panel. They may be caused by impurities, moisture, or oxidation.
In Conclusion
The blog article explains how to ensure and improve the quality of solar panels, which are in high demand as renewable energy sources. It covers the reasons why solar panel quality check is needed, the steps to check the quality during production, and the common defects found during inspections. However finding high-quality solar panels can be challenging, as the production cycle is complex and some suppliers may offer low-quality products. This is why bestsupplier.com, a B2B sourcing platform, offers professional solar panel quality check services and inspection reports. Bestsupplier.com has rich experience and resources in the solar industry and can provide OEM and ODM services for solar products. By choosing bestsupplier.com, you can ensure that you get the best quality solar panels at the best price
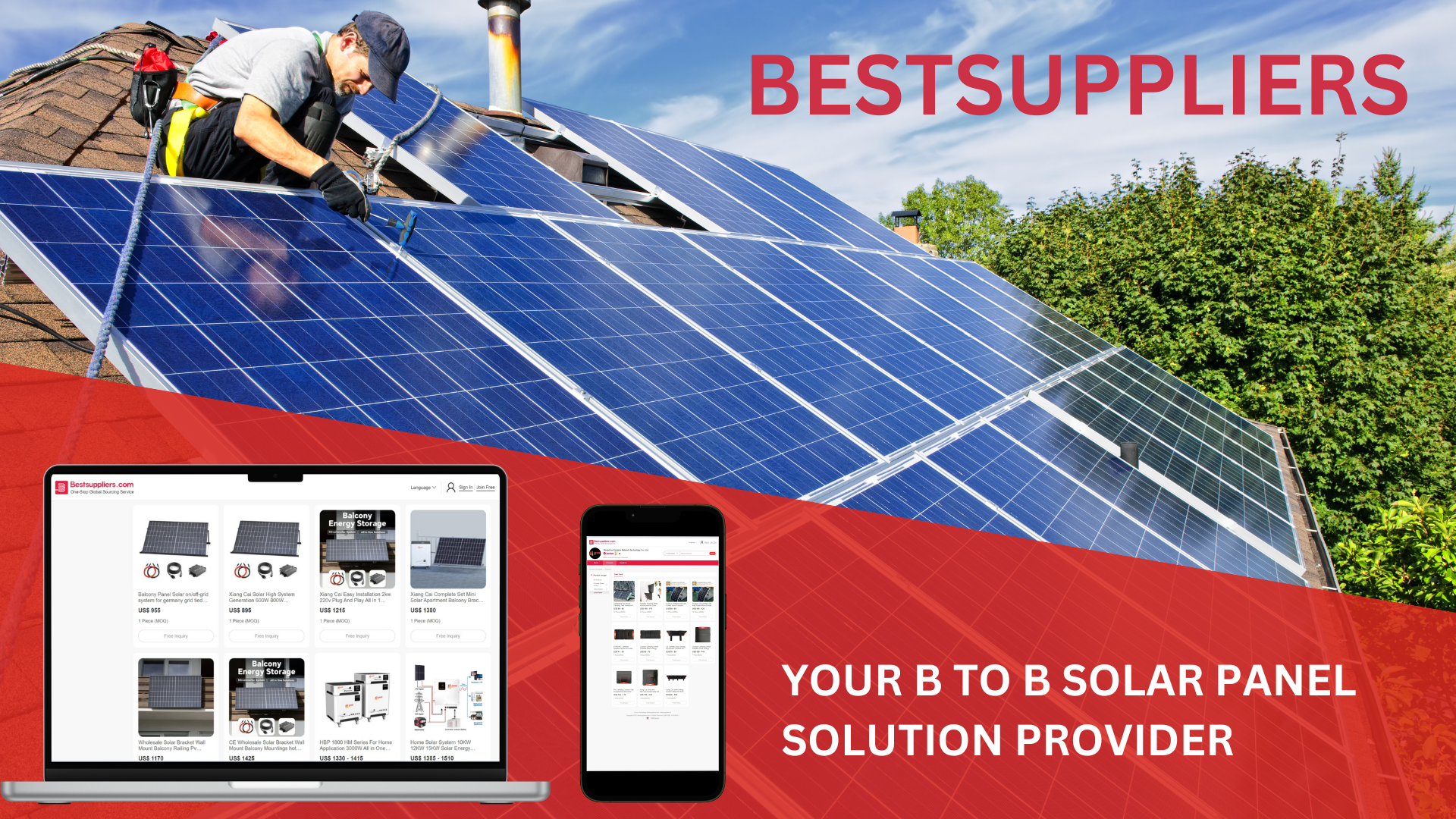